燒結(jié)大煙道高溫段煙氣余熱回收技術(shù)
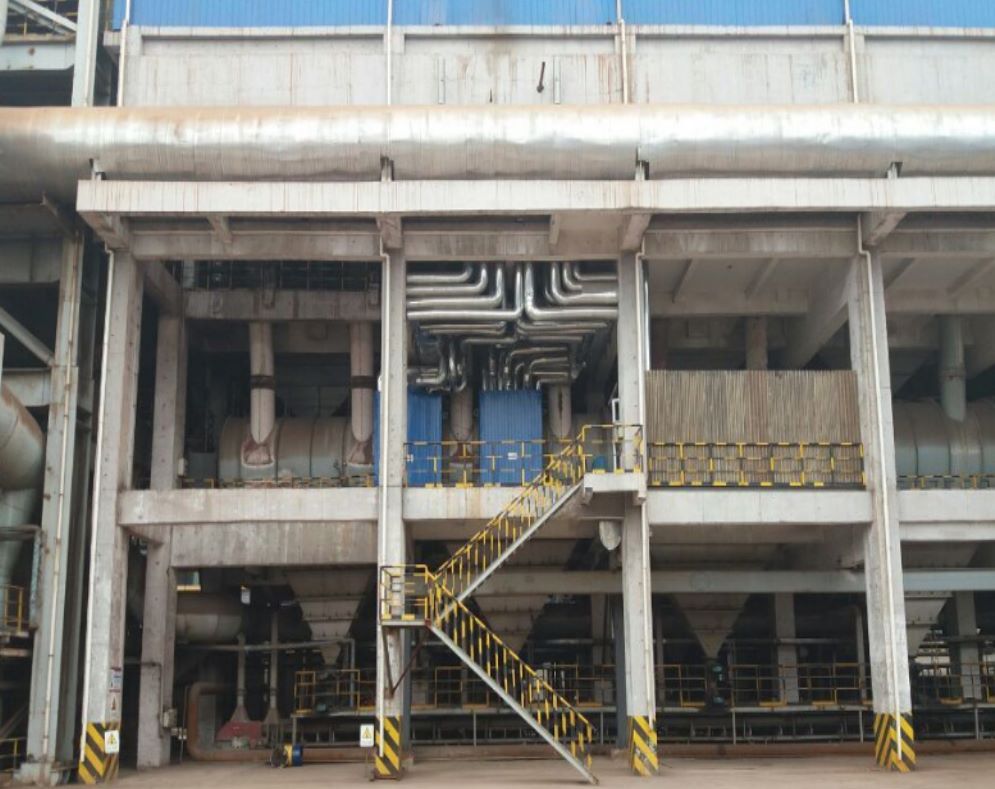
一、燒結(jié)大煙道高溫段煙氣余熱回收現(xiàn)狀
鋼鐵冶金企業(yè)作為國(guó)家支柱產(chǎn)業(yè),能耗占產(chǎn)品成本比例較高,節(jié)能降耗需求迫切。燒結(jié)工序是鋼鐵生產(chǎn)中的高能耗環(huán)節(jié),其能耗僅次于煉鐵工序。其中,環(huán)冷機(jī)廢氣顯熱占總能耗的20%~28%,而燒結(jié)大煙道高溫段煙氣(平
均溫度380~420℃)的余熱資源占總熱能的49%,回收潛力巨大。
目前,余熱回收技術(shù)主要集中于環(huán)冷機(jī)排氣顯熱,但燒結(jié)大煙道內(nèi)的高溫段廢氣熱量回收仍存在顯著空白。國(guó)內(nèi)外鋼鐵企業(yè)絕大多數(shù)尚未對(duì)燒結(jié)大煙道內(nèi)的高溫?zé)煔膺M(jìn)行有效回收,僅國(guó)內(nèi)部分企業(yè)嘗試采用傳統(tǒng)外置式余熱回收裝置。然而,此類裝置存在明顯缺陷:
回收效率低:外置設(shè)計(jì)導(dǎo)致散熱損失大,實(shí)際回收熱量不足;
經(jīng)濟(jì)性差:需額外搭建旁路煙道、閥門及鋼架結(jié)構(gòu),材料與安裝成本高,占用空間多;
上述問題導(dǎo)致燒結(jié)大煙道高溫廢氣回收率極低,大量余熱資源被浪費(fèi),如將此部分余熱加以利用,可將噸礦熱回收量提高30~40kg蒸汽。
二、解決方案
針對(duì)傳統(tǒng)余熱回收技術(shù)的痛點(diǎn),我公司推出內(nèi)置式燒結(jié)大煙道余熱回收技術(shù),通過(guò)創(chuàng)新設(shè)計(jì)與工程優(yōu)化,實(shí)現(xiàn)高效回收與穩(wěn)定運(yùn)行,具體方案及優(yōu)勢(shì)如下:
1. 內(nèi)置集成設(shè)計(jì)——經(jīng)濟(jì)性與便捷性
方案:將余熱回收裝置直接嵌入燒結(jié)大煙道內(nèi)部,直接回收高溫段廢氣熱量,省去外置式復(fù)雜煙道系統(tǒng)。
優(yōu)勢(shì):
成本節(jié)約:減少旁路煙道、閥門及鋼架材料投入,投資成本降低20%以上;
空間高效:無(wú)需額外占地,適配空間受限的改造場(chǎng)景。
2. 專利防磨技術(shù)——可靠性與長(zhǎng)壽命
方案:采用獨(dú)特防磨結(jié)構(gòu)設(shè)計(jì),隔離煙氣顆粒物與換熱管直接接觸,結(jié)合自動(dòng)清灰功能。
優(yōu)勢(shì):
抗磨損:設(shè)備壽命延長(zhǎng)50%,避免非計(jì)劃停機(jī);
低維護(hù):維護(hù)周期縮短40%,適配連續(xù)生產(chǎn)需求。
3. 模塊化配置——快速安裝與生產(chǎn)兼容
方案:設(shè)備采用標(biāo)準(zhǔn)化模塊設(shè)計(jì),支持與現(xiàn)有煙道快速對(duì)接。
優(yōu)勢(shì):
無(wú)縫改造:改造期間燒結(jié)機(jī)停車時(shí)間壓縮至10天以內(nèi);
零干擾:無(wú)需調(diào)整現(xiàn)有工藝,保障生產(chǎn)連續(xù)性。
4. 高效傳熱與低阻力優(yōu)化——技術(shù)性能提升
方案:通過(guò)緊湊流道設(shè)計(jì)與強(qiáng)化傳熱表面,提升熱交換效率。
優(yōu)勢(shì):
高效回收:熱量回收率提升至85%以上,散熱損失減少20%;
穩(wěn)定運(yùn)行:煙氣阻力降低15%,確保主抽風(fēng)機(jī)負(fù)荷穩(wěn)定。
5.?經(jīng)濟(jì)性
投資回收期約一年。
三、總結(jié)
該方案以技術(shù)創(chuàng)新為核心,通過(guò)內(nèi)置集成、防磨設(shè)計(jì)、模塊化配置及傳熱優(yōu)化,系統(tǒng)性解決傳統(tǒng)技術(shù)的經(jīng)濟(jì)性、可靠性、兼容性與效率問題,為鋼鐵企業(yè)提供兼具節(jié)能效益與生產(chǎn)穩(wěn)定性的余熱回收解決方案。